Mastering Welding WPS Standards: Ideal Practices and Techniques for High Quality Welds
In the world of welding, mastering Welding Procedure Spec (WPS) standards is a crucial part that straight affects the quality and stability of welds. As we browse via the complexities of welding WPS criteria, revealing vital understandings and approaches for achieving top-tier welds will be paramount for welders seeking to stand out in their craft and create welds that stand the test of time.
Comprehending Welding WPS Standards
Recognizing WPS requirements is important for inspectors, designers, and welders associated with welding operations. By adhering to WPS standards, welders can produce welds that fulfill the needed mechanical residential or commercial properties and architectural stability. Inspectors depend on WPS documentation to validate that welding procedures are being adhered to correctly which the resulting welds are of top quality. Designers use WPS criteria to create welding procedures that guarantee the durability and dependability of welded structures.
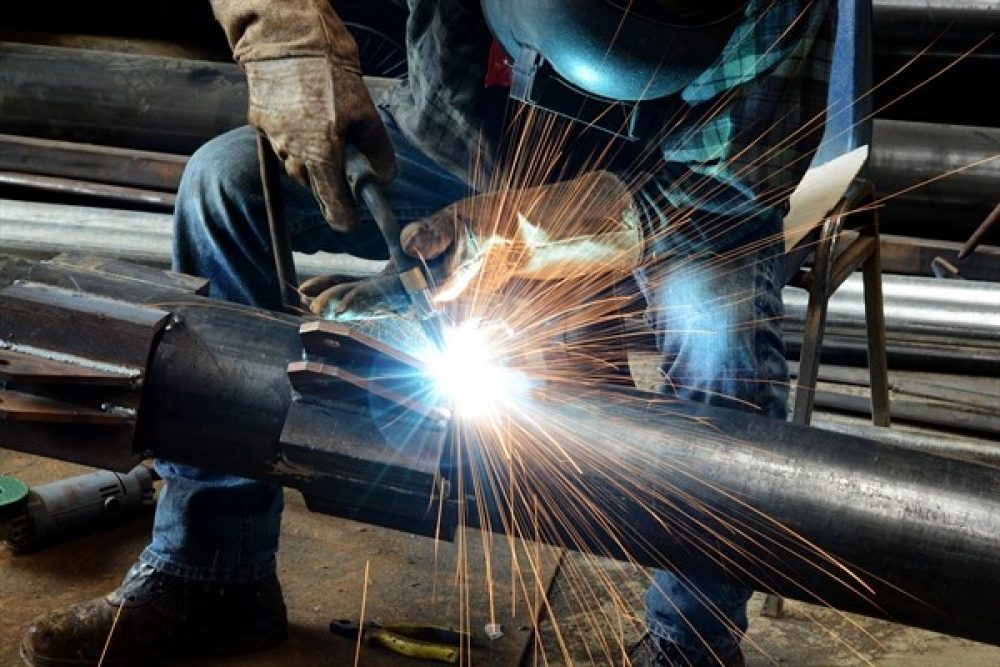

Necessary Devices for High Quality Welds
Mastering welding WPS requirements is vital for welders to successfully make use of the vital tools needed for generating quality welds. The kind of welding machine required depends on the welding process being made use of, such as MIG, TIG, or stick welding. Wire brushes and damaging hammers are important for cleansing the weld joint before and after welding to remove any kind of contaminations that can affect the high quality of the weld.
Key Techniques for Welding Success
To achieve welding success, one should understand the key methods important for generating top quality welds. One critical technique is preserving the proper arc length. Maintaining the electrode at the optimum distance from the work surface is vital for developing solid, uniform welds. Additionally, managing the traveling speed is extremely important. Moving too swiftly can result in insufficient infiltration, while relocating too slowly can cause too much warmth input and prospective issues. Proper adjustment of the electrode angle is one more important technique. The angle at which the electrode is held can impact the grain shape and penetration of the weld. Moreover, making certain constant weapon angle and direction of traveling is vital for uniformity in the weld bead. Last but not least, keeping a steady welding and a click here now steady hand position throughout the process is essential to achieving precision and uniformity in the welds. By grasping these key techniques, welders can boost the top quality of their job and accomplish welding success.
Ensuring Conformity With WPS Requirements
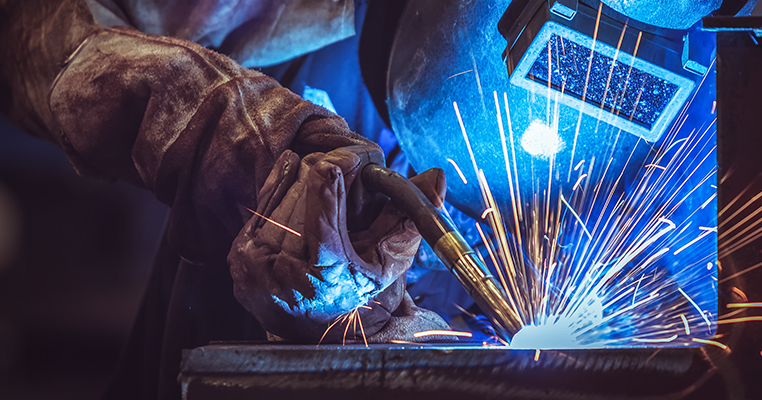
In addition, keeping thorough documents of welding specifications, equipment calibration, and inspection results is critical for showing compliance with WPS requirements. By vigilantly adhering to WPS criteria, welders can make certain that their job meets the needed top quality levels you can check here and contributes to the total success of the welding job.
Troubleshooting Common Welding Issues
When confronted with common welding concerns, determining the origin is vital for effective troubleshooting. One prevalent problem is the existence of porosity in welds, commonly caused by contaminants such as oil, corrosion, or moisture. To address this, making certain proper cleaning of the base metal prior to welding and making use of the proper shielding gas can considerably minimize porosity. One more concern regularly encountered is lack of fusion, where the weld fails to correctly bond visite site with the base material. This can come from insufficient warmth input or inappropriate welding method. Changing parameters such as voltage, wire feed speed, or take a trip speed can aid boost blend. In addition, distortion, cracking, and spatter prevail welding difficulties that can be mitigated with appropriate joint preparation, consistent heat control, and selecting the appropriate welding consumables. By thoroughly understanding these common welding problems and their source, welders can successfully repair issues and attain top quality welds.
Final Thought
To conclude, understanding welding WPS requirements calls for a detailed understanding of the standards, making use of essential tools, and implementing key techniques for successful welds. Ensuring compliance with WPS standards is crucial for producing quality welds and staying clear of typical welding issues. By complying with ideal practices and techniques, welders can accomplish regular and dependable cause their welding jobs.
In the realm of welding, grasping Welding Treatment Specification (WPS) requirements is an essential element that straight affects the quality and stability of welds.When delving right into the world of welding practices, an important aspect to comprehend is the significance and details of Welding Treatment Spec (WPS) standards. WPS requirements give a thorough guideline for welding operations, making certain consistency, quality, and security in the welding process. The kind of welding equipment needed depends on the welding process being utilized, such as MIG, TIG, or stick welding.Attaining welding success through the mastery of key techniques requires a detailed understanding and adherence to Welding Procedure Spec (WPS) requirements.